Mon January 06, 2020
Lucy Perry – CEG CORRESPONDENT
Is staying focused an issue for crane operators? It depends on so many factors, say crane operator trainers and certification sites.
The job site, the employer, the task at hand, even the operator him- or herself, all play a role. OSHA says it falls on the employer to determine if an operator is qualified to recognize and avert risk. And any kind of distraction that results in the operator losing focus is definitely a risk. But avoiding distractions is not a knowledge-based lesson that training participants and certification candidates are ever tested on.
"I am not sure today's job sites create more of a distraction for operators than they have in the past," said Ron Overton, president of Overton Safety Training, Hillsboro, Ore. "I think the operator's mindset is a little different now. With any or most job sites, traffic and distractions are going to occur. You're going to have a job site, an operator, and external factors that aren't related to the job site. You're still going to have all kinds of things on the job site that will affect or distract the operator. I am not sure that has changed all that much."
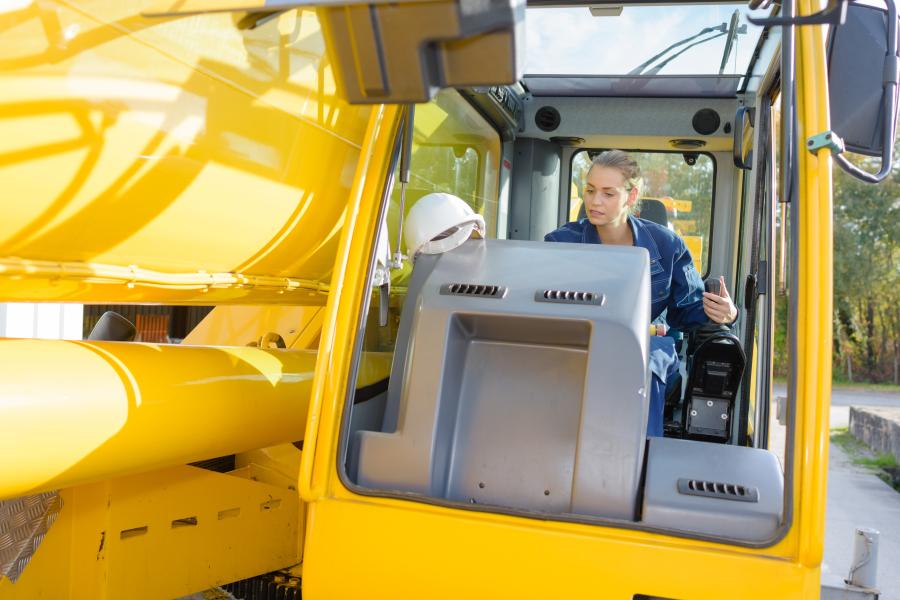
Are crane operators more distracted these days than ever before? Howard Kaplan, who owns Liberty Crane and Rigging Consultants in Phoenix, Ariz., answers the question with a question: How do you quantify distractions? Even more basic: What is the meaning of distraction?
"Is it a cell phone, an LMI, alarms, an anti-two-block alarm, or the backup alarm? If every time you make a lift somebody's hitting an air horn, is that a distraction?"
There are so many sights and sounds, so much activity on a job site an operator can get complacent, said Kaplan.
"Newer crane cabs have Bluetooth systems, radio remote, all kinds of bells and whistles to contend with."
Plus, operators have cell phones.
"I've had customers who see an operator's head tilted holding the phone to his shoulder while operating a crane and it doesn't look good," said Kaplan. "I agree the operator shouldn't be on the phone, but the law says ‘he shall not be distracted.' So, if he's on a lift he shouldn't be on the phone. If he's using the phone for signals, it should be OK."
Kaplan believes a cell phone is "every bit as effective" as other means of hands-free signaling.
"If I have a good headset, it's all hands free, so I don't have to push to talk. It's good two-way communication, and that's what I teach."
Dealing with distractions for the most part leads back to company policies and procedures, believes Overton.
"I'm not sure a cell phone is a distraction as long as a company's policy and procedures are being followed."
For example, company policy might state an operator can't use a cell phone except on breaks or pauses when the load is not in the air. Some operators use cell phones as handsfree signal person methodology for communication which meets OSHA's requirement that the signaling communication device be hands-free. "The employer should have a policy in place, which addresses this issue" Overton added.
Qualification, Certification, Distractions
Kaplan said OSHA rules specify when to signal, what to say, and how to say it.
"If the signal person and I as the operator have a conversation, if we get into a rhythm, if we understand what the other one wants all the time, I'm not suggesting we change any language. If I'm lowering the load and he likes that speed and he can control the speed as a signal person, just tell me that."
He believes OSHA's signaling rules can be confusing, though, because the words chosen are not consistent throughout all commands.
For certification, Kaplan teaches the letter of the law. For operator qualification, he teaches the law in a way the crane operator wants to hear it. Overton, too, offers two types of operator training. Initial operator training and qualification for companies takes one format, while preparation for national certification is somewhat different. When preparing for the national safety exam operators are responsible for all things in their control, including the load once it's off the ground, said Overton.
"The OSHA rule falls on the employer for qualification training. Operators have to be able to recognize and avert risk. The issues of recognizing risk would be applicable to the specific job site, the equipment being used and/or the craning tasks being performed," said Overton. "They need to understand the risks involved, and certainly distractions are a risk. It would be included in the employer's internal training program related to tasks and the use of that equipment. When we are asked, we cover these issues with the operator during qualifications training for an employer."
Policy might specify that an operator can't eat or drink in the cab unless the load is on the ground. Maybe he's restricted from talking on his cell phone unless he's on break. Another distraction many employers address these days relates to an operator's being sedentary for long periods of time. People have a tendency to relax and lose focus if they're sitting in an area for a large period of time. So often, stretching, moving arms and legs and standing up at specific intervals are required by an employer.
"Some companies will write policy to state an operator has to take mandatory breaks at specific intervals while operating," said Overton."
The operator has to stand-up or get out of the cab. Maybe they can stand out on the carbody, and stretch, walk and make the brain work before they get back into the cab. They will often do this between long durations of operation, because when you're sitting in a chair or standing in one position, you can only sit there for so long and then you have to get moving again."
Movement gets the brain to reset and gets the operator back to being focused on the lifts while still being aware of everything happening around him, as opposed to being kind of oblivious.
Overton said his training staff, when asked, has provided consulting services that included discussion with class participants about the mental mindset, outside distractions, impairment and lack of sleep. He said dehydration also is a serious risk factor for distraction, and many companies have dehydration prevention steps in place.
"If you're dehydrated, your brain's is really not functioning well. All those things play into being distracted and losing focus."
Kaplan believes that everybody and anybody can be distracted. But he puts a different perspective on it: All the distractions can actually improve an operator's ability to deal with them, as they become a part of the worksite.
"I think it's amazing what someone can become used to," said Kaplan. For instance, "today's operator cabs are significantly different than 50 years ago, with access to operator aids, comfort, ergonomics, and noise insulation. All that helps" reduce the distractions, he said. "My whole take is, concentrate on your job. Do your job. Most importantly, it's a good idea to know how to do your job, and then it goes back to training." CQ
How Do You Train Operators to Stay Focused on the Job?
Ron Overton, president of Overton Safety Training Inc., has a goal to assist operators with focusing on the task at hand, maintaining safety and preventing distractions.
OSHA Federal Regulation 29CFR1926.1427 requires the employer to provide operator training in the form of a combination of formal and practical instruction and [the ability to] learn how to recognize and avert risk necessary to operate the equipment safely; and an employers operator evaluation, which includes the skills and knowledge and ability to recognize and avert risk necessary to operate the equipment safely; [and the] ability to perform hoisting activities required for assigned work.
"One of the possible methods or methodology for employers to instruct operators to ‘recognize and avert risk' would be to ensure the operator understands the importance of taking appropriate steps in minimizing or mitigating distractions, which might hinder or affect their focus while operating the crane."
Here is Overton's informal list of "potential roadblocks" that operators may experience that might affect their focus, and how to mitigate or prevent the roadblocks:
Worksite-Related
- External noise. Possible preventive measure: Hearing protection
- Traffic proximity, equipment and personnel. Possible preventive measures: Cones, barricades, working area markings. Create a lifting corridor
- Other equipment operation. Possible preventive measures: maintain ongoing communication and awareness of and with other equipment operators. Using cones, barricades, working area markings. Create a lifting corridor if possible.
- Electronic communication with others. Possible preventive measure: Limit non-essential communication while operating
- Temperature in cab. Possible preventive measure: Appropriate ventilation, heat or cooling
Personal
- Music, headphones, earbuds. Possible preventive measure: Restrict use and follow company policy/procedure.
- Smoking. Possible preventive measure: Allow only during breaks and away from the crane.
- Cell Phone. Possible preventive measure: Other than use for signaling, allow only during times when load is grounded, or only during breaks
- Eating or drinking while operating. Possible preventive measure: Allow only during times when the load is grounded, or only during breaks
- Mindset, outside personal issues, Possible preventive measure: Understand safety of others is involved, actions will affect others.
- Mental impairment. Possible preventive measure: Follow company substance use/abuse policy or program
- Lack of sleep. Possible preventive measure: Instruct on the importance of getting appropriate number of hours of sleep
- Dehydration, lack of nutrition. Possible preventive measures: Instruct on the importance of hydration, and following company requirements for mandatory hydration. Instruct on the importance of proper nutrition and fuel for their mind and focus.
- Extended sedentary (sitting) operation. Possible preventive measure: Program of pre-use stretching and movement/rotation of arms to facility blood movement and warmup. Mandatory breaks between periods of operation with required standing, stretching and movement/rotation of arms to facility blood movement.
- Clothing. Possible preventive measure: Instruct on wearing levels or types of clothing appropriate to the experienced temperature and humidity and to maintain relative comfort while operating.
Outside
- Weather, temperature, wind, conditions. Possible preventive measures: Shutdown in hazardous weather, lightning and/or excessive wind. Follow company policy for working during extremes in temperature or external conditions.
- Visibility. Possible preventive measure: Utilize qualified signalperson/ spotter when required and maintain proper visual or verbal communication at all times.
- Noise. Possible preventive measure: Utilize approved hearing protection that does not hinder ability to respond to verbal instructions or warnings.