Mon January 13, 2020
Lucy Perry – CEG CORRESPONDENT
With just a few months to go before the new ANSI A92 standards are officially in effect, the access industry is still in preparation mode. Aerial manufacturers are putting the final touches on new machine design and safety features and, along with professional organizations, are dedicating time and energy to training for best MEWP operating practices.
The new standards, in the works more than six years now, are written for owners, operators and supervisors of mobile elevating work platforms (MEWPs), scissor lifts and under-bridge inspection machines. The goal behind the updates is to bring North American equipment standards closer to international standards.
"Give credit to manufacturers and organizations like IPAF," said Mark Hinkel, president of both Hinkel Equipment Rental Associates, Huntingdon Valley, Pa., and the Institute of Aerial Lift Safety, Philadelphia, Pa. "People worked on the standards and made them sensible. The whole idea was to bring American standards more in line with standards throughout the rest of the world. I think it will improve trade between Europe and Canada and the United States. Because as manufacturers were building machines and moving across the world they weren't sure what they needed to do to be in compliance internationally."
An Eye on Safety
MEWP manufacturer Genie, a Terex brand, has outlined what every company that uses the equipment needs to know about A92 standards changes, starting with required development of a documented safe use plan that includes a detailed site risk assessment, as well as rescue plans everyone must be trained on.
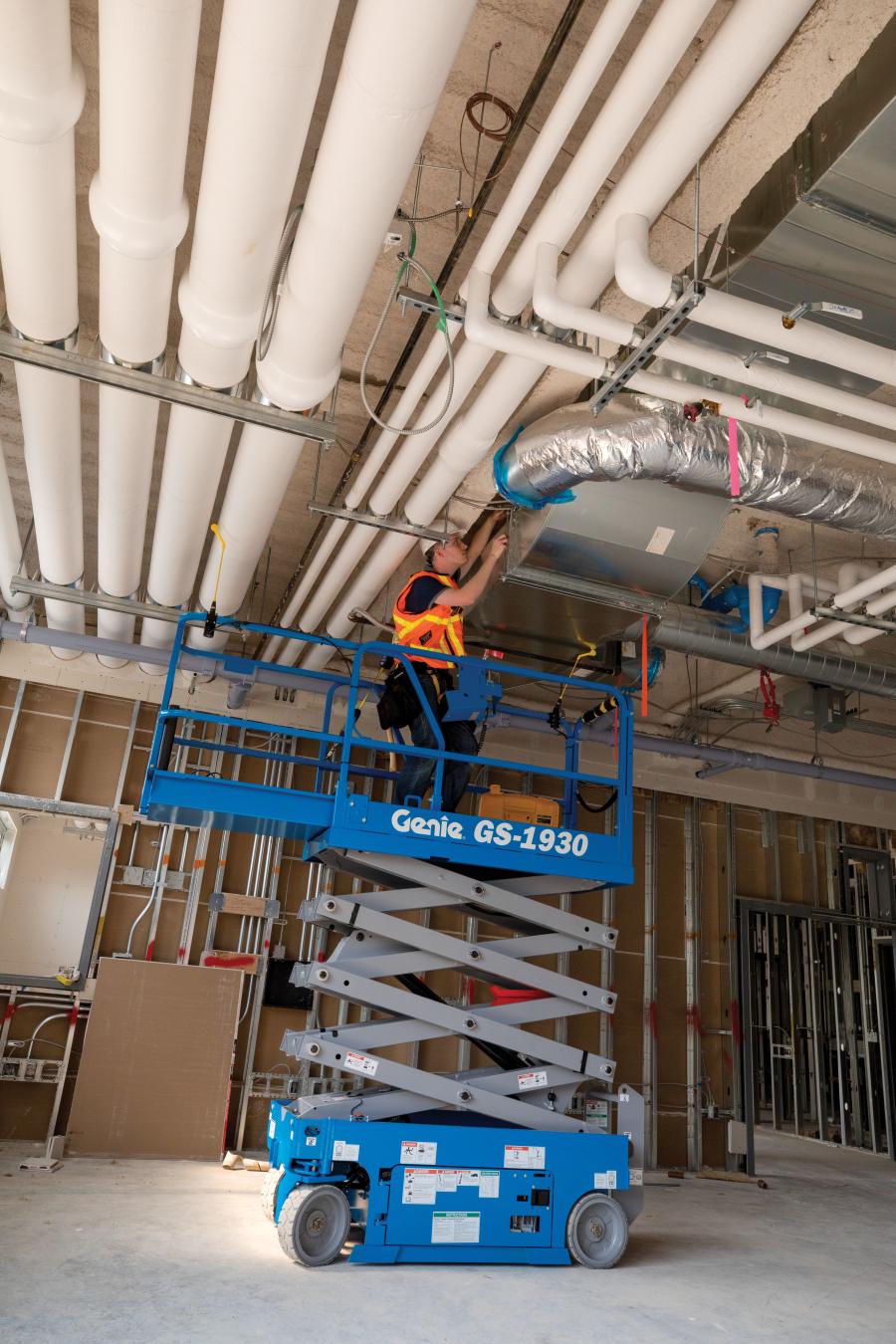
"Anyone who directly supervises a MEWP operator must also receive training. Even the operator will now have the responsibility to provide limited training to any occupants that will be accompanying them in the platform," reads the blog post by Scott Owyen, Genie training manager.
The safe use program specific to MEWPs must include a site risk assessment to identify hazards, evaluate risk, develop control measures and communicate with all affected persons; rules for selection, and use of a suitable MEWP and associated equipment; access, preparation and maintenance of the site including assessment that the support surface is adequate for the machine's weight; MEWP maintenance including inspections and repairs; informing the operator of local site requirements and warning and protection against hazards where the MEWP will be operated; a trained and qualified supervisor to monitor the operator for standards compliance; prevention of unauthorized MEWP use; and safety of persons not involved in the operation of the MEWP.
"The risks associated with the task specific to MEWP operations must be identified. These might be associated with the location where the work is to be carried out, the nature of the MEWP, or the personnel, materials and equipment to be carried," said Owyen.
Once identified, the hazards and risks must be eliminated or mitigated, and the MEWP user must communicate the results of the risk assessment to all parties involved.
"The safe use standard, A92.22, now is providing a lot of advice to manufacturers, dealers, users, operators and other entities as to what is expected of them," said Hinkel. "It provides a lot of pinpoint detail on responsibilities, such as annual and frequent inspections, pre-shift inspections, maintenance procedures, methods of operations and risk assessments."
He said a huge percentage of the construction industry has no idea of the detail in these standards.
"It's really necessary to get the word out so some of this can create awareness within the industry of user responsibilities," he said.
The user also must develop a written rescue plan in the case of machine breakdown, platform entanglement or a fall from the platform. It must be put in writing and become part of the company's training manual. Further, MEWP occupants must receive training on procedures to follow if they fall and await rescue, or witness another worker's fall. The plan must limit the time that a restrained worker hangs suspended.
Training Across the Board
Though MEWP operator training won't change much, there are additions to the training rules. Training must now also cover proper selection of the correct MEWP for the task; a workplace risk assessment, including rescue planning; and occupant training. Supervisor training also is a new requirement, and it falls on the user to ensure all personnel who directly supervise MEWP operators are trained to the same general training that the operator is required to undergo.
Another addition to the standard are rules for occupant training. The operator is responsible for ensuring that all platform occupants have basic knowledge to work safely on the MEWP. They must cover the use of fall protection and the location of fall protection anchors; how their actions could affect stability; safe use of any MEWP accessories; site-specific work procedures related to MEWP operation; hazards related to the task; manufacturer's warnings and instructions; and the knowledge to operate the controls in an emergency.
"The A92.24 standard covering training requirements is very nicely detailed and is now offered to everybody to understand what is really needed," said Hinkel. "The standards are best practice, and are incorporated by reference in OSHA. If folks are running their jobs and not using best practices, in the event of an incident and accident, they're going to be found at fault for some portion for not following best practices as the industry knows them."
A Picture of Machine Health
According to the updates, users are responsible for guaranteeing personnel are trained to inspect and maintain the machines per manufacturer's recommendations and industry standards. If a MEWP is being rented, the owner must identify the entity responsible for inspections and maintenance as the standard outlines. This includes frequent and annual inspections. When a dealer rents a MEWP, the user absorbs responsibilities.
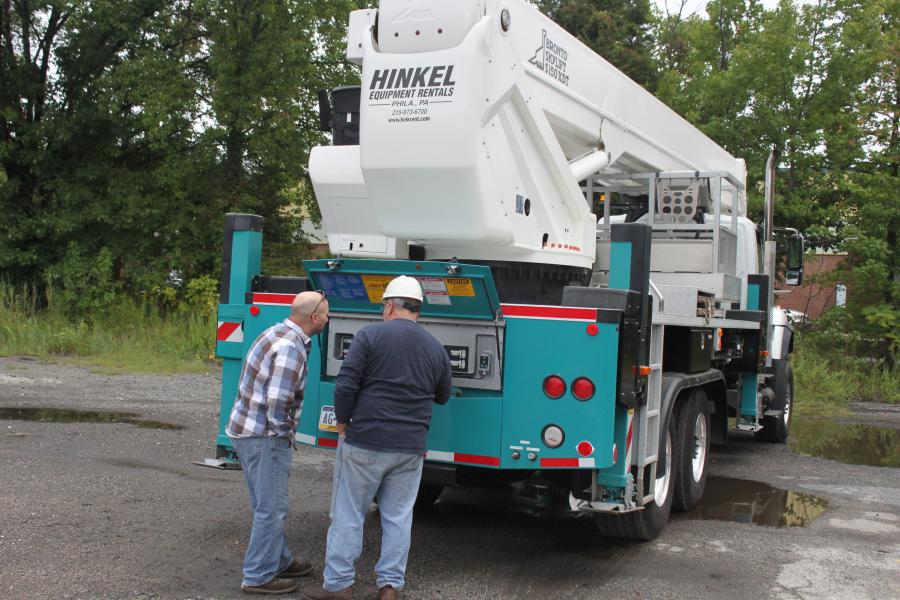
Hinkel operates as a Bronto dealer, and he believes that the legal system is driving a lot of the standards changes. He said the mindset that there isn't enough time to conduct training and inspections has been pervasive in the industry for some time.
"It's one I try to make a concerted effort to dispel because that's just setting things up for a problem."
Hinkel Equipment Rental Associates performs equipment familiarization sessions for the Bronto machines the company rents to customers. The dealership also offers operator training through the Institute of Aerial Lift Safety, which is an IPAF training center.
"We do scissor lift, boom lift and vehicle-mounted aerial training," Hinkel said. "In our rental business, if people tell us they don't want the operator familiarization, we turn down a significant amount of work, probably 5 to 10 percent of our jobs, because of this."
Keeping Your Weight in Check
The new ANSI A92 standards include directives for equipment manufacturers. New models must have a gated entrance to the work platform, some models will have reduced lift and load speeds, and MEWPs on rough terrain will have to have foam-filled or solid tires, said Mark Gates, in training and product support for Toyota Material Handling of Northern California.
If a safe load limit is exceeded, an alarm will sound and a sensor will prevent normal operation, he noted in a TMHC blog post about the standards updates. All new equipment will come with a tilt sensor system, which will disable boom functions if the machine exceeds slope limit.
These safety measures will put a crimp in new-machine sales, warned Dave Brown, regional sales manager, Southeast region, of United Rentals. Every boom or scissor lift has a basket weight capacity. He said for most booms, if they have a jib, that capacity is usually 500 lbs., and for a straight boom it's 750 or 1,000 lbs. For a scissor lift it's about 400 lbs., and a rough-terrain scissor, about 1,500 lbs.
"In December 2019, every new manlift manufactured will have a device on it that tells you how much weight is on that platform. If you're one pound over, the machine will not work."
While he understands it's a safety enhancement meant to save lives, it's a big deal from a rental standpoint, he said.
"If somebody's going to boom with the jib and there are two men who weigh 220 lbs. apiece in the basket, the MEWP will not operate."
Every machine made prior to 2019 will be grandfathered in. As Toyota Material Handling of Northern California pointed out, existing equipment does not need to be retrofitted to meet the new standard.
"This is going to cause a real problem because customers want the newest machine we've got available. Now, nobody's going to want the newest we've got because of the weight-capacity limiter," said Brown. "Over the next five years, every machine will have that function, and it'll make people change how they work with manlifts."
For example, he said, most steel erectors order machines with a jib because it makes their work more flexible in that it offers them an extra elbow to boom around a structure.
"The problem is, you'll lose capacity by half because when you use that jib it lowers what you can lift. The jib weakens the lift capacity. So, it will change the rental landscape because it will just cost the customer more money. With more weight capacity, if he needs up-and-over function he'll have to rent a bigger machine," said Brown.
Hinkel of the Institute of Aerial Lift Safety said every machine manufacturer has to incorporate some platform load-sensing function which will cut motion in the event of an overload. He said Bronto has had a version of a load alarms for 30 years.
"In 2001, they started incorporating an overload cutoff on many models they built. This A92 design change simply means self-propelled machine manufacturers and scissor lift manufacturers are now required to incorporate overload sensing and motion cut-off functions," something he said was talked about when the new standards were being developed.
"It can create more service issues for rental companies and dealers. But the benefit of having fewer overload incidents is well worth it. If we save one life, prevent one injury, it really helps" said Hinkel.
People have been overloading equipment for 50 or 60 years, since the first bucket truck aerials were designed, he noted. Brontos are equipped with a black box, which not only cuts the motion, but records the overload incident date and time so the dealer or manufacturer can see there was possible damage to the machine.
"In the event of an accident you could go back and see what the operator did in violation of the way we would use the machine, and what may have contributed to the incident or accident. We have had situations where people when up, overloaded the platform with tools, and it stopped," said Hinkel. "The manufacturer directed the user to remove gear or materials from the platform. They did that, and it worked again. In a lot of cases, they were working incorrectly to begin with."
To Learn More
For anyone who hasn't gotten up to speed on the new standards in the United States and those for use in Canada, there are several resources available to you. Here are a few:
- On its website at genielift.com, Terex brand Genie offers white papers, blog posts, quick reference guides, and question-and-answer events.
- JLG has created an education site, www.jlg.com/en/destination/ansi, to help users better understand and comply with the new standards.
- Toyota Material Handling of Northern California has dedicated a blog post titled "New ANSI Standards for 2019 What You Need to Know" at https://www.tmhnc.com/blog.
- IPAF issued four guides, for dealers and users, addressing ANSI standards for United States users and the CSA standards for Canada. Visit www.ipaf.org/resources, or contact USA@ipaf.org.
- The Institute of Aerial Lift Safety, at www.aerialliftsafety.org, will educate, train, and offer general information on the new A92 rules. CQ